SIPs News
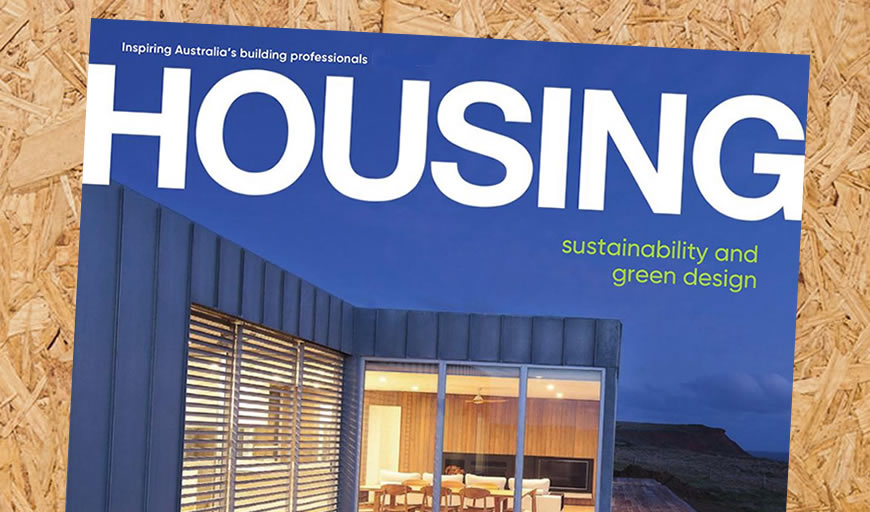
Housing Magazine Interview
-
in SIPs News
Our Managing Director, Rob Vis, was interviewed by HIA's Housing Magazine for an article in the September 2020 issue. Rob gave a great insight into what SIPs and SIPs Industries are all about.
You can see all the Q & A's below or check out the full article on the HIA website - https://hia.com.au/housing/people/2020/rob-vis-insulating-the-future
Rob Vis
Q1. When it comes to sustainability in building what are you most passionate about?
A. Our focus and passion are sustainable healthy living and so we are driven to provide one of the most sustainable building products that offers energy efficiency, comfortable living conditions for the end user without affecting the living environment.
Our product will assist Designers and Architects to achieve their goal of zero net Carbon, off grid, to Passivhaus, and living buildings using sustainably sourced materials.
Q2. In what ways does your business practice sustainability in its operations?
A. Sustainable buildings are the hallmark of economically sound business decisions, thoughtful environmental decisions, and smart human impact decisions..
Materials we source..
Our timber is sourced from 100% renewable managed plantations using fast growing soft woods that are easily replenished and perfect for use in the manufacture of OSB (Oriented strand board) The entire log is used and therefor there is no wasted wood. Certified sustainable forestry and certified suppliers ensures wood is not sourced from illegal harvesting, or originates from regions where civil or fundamental rights are violated, Forrest with high protection values, genetically manipulated trees, or originates from forests that will be converted or non-forestry uses
Recycle.
We recycle waste or off cut at the factory and careful design and manufacture process minimises any waste. What we send to site stays on site. Very little if any rubbish is generated as all product are cut and engineered to fit reducing the need for rubbish sent to land fill from building sites.
Sustainability through Service.
We liaise and collaborate with Designer, Engineer and Builder during the design process. The aim is to reduce carbon footprint, reduce steel structure, improving real thermal performance, reducing thermal bridging, air leaking through the structure and managing moisture.
Sustainability through service has the added benefit of reducing cost complexity during the build process.
Q3. Can you explain how structural insulated panels help to produce sustainable housing?
A. Sustainable housing could mean accessible, renewable, cost effective, easy to assemble, complementary to other sustainable products and provide energy efficient outcomes that are socially acceptable.
Energy efficient homes can be more expensive to build, demand specialist trades, materials and builders so a need to change the way do business if we are to remain competitive.
No one is a big fan to change, taking, time, effort, re-training, initial cost. The building industry is no different, but chance is a constant we must embrace.
SIPs extract value across a range or areas through the construction process (simplicity, speed and savings) and post completion (more energy efficient homes that comfortable and environmentally responsible)
Construction.
SIPs Simplicity provides for a much faster and more streamline building process allowing saving in overall labour, scaffold, less waste, lower theft, less steel, and reducing builder overheads. This allows for a high-quality product at a competitive price.
Post construction.
SIPs have a direct impact on thermal performance providing a higher real-world R value, by significantly reducing thermal bridging (can be as high as 24% within the walls alone through studs and gaps) and reducing are leakage. New regulatory changes proposed provide for pressure testing new buildings and on the way.
Looking at just air movement, the average Australian home may leak up to 20-30 time its volume per hour through its structure, so a lot of energy is leaving the building with more energy required to heat or cool. SIPs homes can reduce this to as low as 0.25 air changes and with the use of air exchange units we are able to recover up to 85 % of the energy whilst introducing clean fresh air to the building as needed whilst maintaining simplicity in construction. This offers massive performance gains and cost savings to the end user.
Q4. Is it suitable for all climate zones?
A. SIPs panels have been associated with cold climate housing initially used in North America since the 1950’s.
It cost 3 times more to cool a home than it does to heat it. The biggest growth market has been warmer climates across the World with power cost on the rise and tipped to double over the next 5 Years.
Sips Industries are in all climate zones, States and Territories from the Snowy mountains in Dinner plain to the Desert house built on Alice Springs being an off the Grid build. SIP’s has demonstrated its ability to adapt to a range of climates and environments being some of the more hostile to build and live in.
Q5. Are you seeing an increase in demand for your product and for sustainable products/design in general?
A. We have seen steady growth and an increase in demand Australia wide from multiple market segments. Empty nesters wanting to take positive action on reducing their net living costs moving into retirement to young couple wanting to put more money on the mortgage than on utilities bills.
There has been significant uptake by Architects focussing on better more sustainable products yet maintaining beautiful Architecture.
Commercial builders are adopting SIPs for its speed of construction, reducing site costs and overheads as this affects them directly.
We have also seen take-up in the Government sector assisting them to meet their triple bottom line targets (cost, environmental and social) and be seen to develop real environmentally responsible and healthy buildings.
There is a clear shift in demand for better buildings
Q6. What are some of your sustainability success stories since you established SIPs Industries?
A. We are in the thousands of homes across Australia since we opened 2010 and some more exiting builds have achieved best practice in range of areas.
Desert House, near Alice springs, a custom built unique Architecturally designed off the grid dwelling.
The Home was designed and Engineered in NSW, SIPs manufactured in WA and built by a local builder in the NT. This home won several National awards and accolades demonstrated our ability to team up design and construct sustainable dwelling Nationally with high level of detail required to achieve best practise.
Mining sector remote tyre monitoring and service centre Port Hedland WA. The client brief was to build a sustainable best practice remote office embracing its environmentally responsible approach to doing business. This building is the lead example in best practice and was officially opened by its overseas and national team. The client was very happy with the result exceeding expectations in a challenging remote cyclone rated region.
Joondalup Childcare centre WA. A clean toxic free safe and quite environment for little guys. The brief was to assist in providing a comfortable safe building for children and meet a very tight deadline for handover. This was met and on budget. After 6 year in operation, the feedback from staff and users has been very positive saying how quite and comfortable the building is to work in and efficient to operate. Its great to be involved with such project
Q7. Are there any exciting projects or research and development that you are involved in now?
A. Currently we are working with Industry, in apartment and single residence dwellings to better communicate the effect of condensation causing damage to wall and roof systems in the form of moisture build up within buildings that are increasing insulation layers to meet building codes.
This is becoming a significant problem with limited education in this area. New Zealand alone had over $20 Billion worth of damage to homes labelled Leaky homes or Sick home syndrome.
Moisture can build up on cold external surface on the building due to vapour within the building penetrating the structure, a wet construction period, or leaks.
If not expelled from the structure, moisture will build up on the inner face of the external cladding causing mould and “Sick Building Syndrome”.
SIPs industries are focused on delivering long term solutions to building and ensure the building remains healthy, which in turn affects the occupants. Mouldy homes can cause many human health problems such as CIRS (chronic inflammation of the respiratory system). SIPs External wall and roof panels are lined with a breathable lining. This allows moisture to escape and evaporate away from the building along with correct detailing. Sips panels are proving to be a leader in best outcome in the area.
Q8. What do you think sustainable building will be like in residential construction in the future? (e.g. More prefabrication? Greater uptake of Passiv Haus? Other?)
A. Drivers for sustainable housing, coupled with unique Australian innovation, outdoor living and easy-going lifestyle, I see great future in what we can do as a building industry, with more focus on better living. We will embrace many systems and principles such, Solar, Battery, better materials new technologies but with our own spin that is more conducive to who we are, our lifestyle and environment.
We may see more of a hybrid approach to building off site (flat pack) rather than full prefabricated houses. Shorter lead times and higher performance at a better cost point managing overhead and logistics are still a challenge the development of smaller narrow lots will push hybrid with limited space on site and shorter build times.
Q9. Is there more that the industry and manufacturing could be doing to produce sustainable products and incorporate sustainability into their production processes? How so? (consider commenting on the constraints that make it difficult to achieve results and ways to overcome them)
A. Australia really needs to get on and instigate change as one of the worst environmental performers in the developed world, there is significant opportunity to improve our position. Motor vehicles are not safer and greener because the industry thought it was a good idea. Good Legislation and customer focus for better environmentally responsible housing will demand that industry keep up and work collaboratively. Responsible manufactures are demonstrating how it can be done, now we need the will and leadership to instigate real change.
Q10. The impact of coronavirus is a hot topic at the moment. Do you think it will influence the way we design and build eco-friendly housing to improve occupant health and wellbeing?
On observation, we are seeing a shift in attitude that is leading to a change in behaviour. People are recognising that that Covid is as direct result to how we have managed our environment, its fragility and how it is directly impacting us as individuals.
People are asking the right questions, wanting to make a difference to our environment beyond just saving money on home utilities, it is the need to be kind to our planet, our home.
We are becoming more willing to invest in our future and the wellbeing of future generations. Companies are seeing the benefit of being environmentally responsible. I would expect to see some benefit from our misfortune though we need to convince or leaders of the fact.