SIPs News
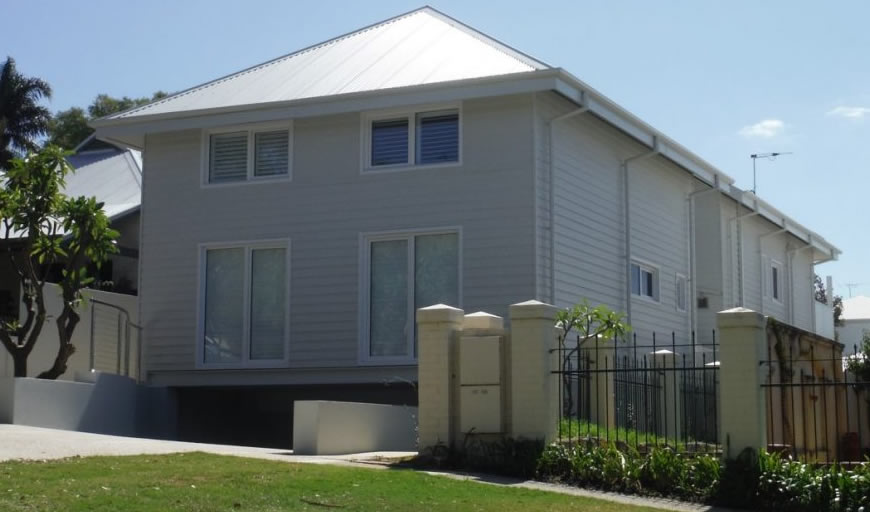
SIPs Passivhaus
-
in SIPs News
Passivhaus is a rigorous, voluntary standard for energy efficiency in a building, reducing its ecological footprint. It results in ultra-low energy buildings that require little energy for space heating or cooling.
We spoke with Roger Joyner, the building designer and Passivhaus Consultant who was responsible for designing and achieving passivhaus certification for the SIPS built home in Cottesloe . . .
What is Passivhaus? - Explained in 90 seconds.
Passivhause is certified in three categories, Classic, Plus and Premium. Each requires the same building performance, Classic being the traditional Passivhaus, Plus requires the building to produce additional energy, up to what the building will consume, and Premium requires the building to generate excess energy that is redistributed back to the grid.
The Passihaus project in Cottesloe by Roger Joyner and Consortium Builders, built with SIPs panels, achieved the first Passivhaus Premium Certification in Australia, and at the time was one of only ten in the world. This home has been breaking building records since its first blower door test when the building was simply SIPs, Windows and Doors and was tested to be the most airtight building in the southern hemisphere at the time.
During the design process, Roger approached SIPs Industries for our quality product, and personal expertise on the subject of air-tightness, thermal insulation and ventilation.
And whilst we were involved in the testing, detailing and construction of this project, we had some questions for Roger.
You’ve said that air-tightness is key to building performance, and in particular to achieving Passivhaus certification, are there many structural building methods or products in the WA market that can easily achieve airtightness without the need for additional air-tight membranes?
Wet plaster has a good airtightness but involves another trade and would be susceptible to movement on a lightweight structure. In lightweight systems the permeability of the internal cladding is paramount if it is to be the airtight layer and we know that there have been issues with OSB type materials, like the facings of structurally insulated panels when used individually. The composite nature of your SIPs panels with two OSB facings and two glue layers in addition to the EPS core have demonstrated that this is indeed a very suitable way to achieve good airtightness.
You chose SIPs Industries panels for this project, we know the benefits of SIPs in these situations, air-tightness, insulation, limited thermal breaks. Were there other benefits of SIPs in this build and were you expectations achieved?
When we started to design the Cottesloe house I wanted it to be repeatable and I wanted to utilise as many local materials and manufacturers as possible. We did not want to reinvent the wheel or necessitate the use of unfamiliar systems or trades. We wanted to utilise a system that had been tried and tested in Europe to give the best chance of success in the first project. Finding a way to eliminate the thermal bridge at the intermediate floor level and not break the airtight layer on the inside face was a great bonus.
The average home in WA leaks a up to 15 volumes of air per hour, this home was tested to leak 0.25 volume of air per hour. SIPs panels, with the meticulous detailing of the builders including airtight tapes at junctions made this massive achievement happen. It is impossible to compare a building like this to traditional building methods such as double brick and timber and steel framed construction, but was it difficult to adopt a newer construction method and does it cost much more, if even to build a better performing home and not specifically to Passivhaus standard?
Passivhaus is not prescriptive when it comes to construction systems. It just wants you to achieve continuous insulation and an airtight layer, in our , on the inside. It is possible with double brick but you do need to include the insulation and that is going to increase the wall thickness so there are more space economical options. All Framed construction, and SIPS, need an external wrap for waterproofing as all claddings are ostensibly just rain screens but those will achieve this only with an additional membrane on the inside for airtightness. The use of SIPs eliminates this additional process and is sufficiently airtight.
This particular build has achieved Passivhaus Premium, of the three Passivhaus standards, Classic, Plus and Premium; Premium is the holy grail. Meaning the building is so efficient, and generates more renewable energy than it needs. The excess energy is being shared with neighbours. Can you give us some more insight into how the building has ‘too much’ energy, and how does the home share the excess energy?
The energy use requirements in Passivhaus are the same across all standards. The difference in the levels is the amount of renewable energy generated on the site. This reduces, or in this case, eliminates the need for fossil fuel generated electricity (once batteries are installed) and the consequential greenhouse gas emissions that are causing climate change. In producing more energy than is needed for the occupants to live comfortably the house returns electricity to the grid which is then utilised by its neighbours. Meaning that they are not using fossil fuel generated electricity and are eliminating the massive losses in extraction, generation and transmission from our remote supply system.
Can you share any other insights in relation to SIPs and how alternative and newer construction methods can achieve far more efficient and comfortable homes, particularly the ease of adopting these principles and I feel the general consensus across WA is that it is too difficult to get builders, designers and engineers to adopt these ideas?
We have to be very careful of new concepts, especially where customers are expecting a good lifetime of use from their major purchase. There have been systems marketed here with little or no trial and no history of longevity. Some are bound to fail. SIPs have been around for many years in Europe(the US and Japan) and the system has been used extensively in achieving Passivhaus buildings. This is the reason we agreed to build the first Passivhaus in Western Australia using these locally made panels from a company whose owners have a long history of working with this system.
If you're looking for a ‘passivehaus consultant in Perth’ you can't go past Roger Joyner. You can view his website at passivhausperth.com.au.